- 产品简介
- 产品特点
- 产品规格
- 产品尺寸
- 资料下载
- Solid shaft with key
- Solid shaft without key (C0 - C5, starting at C6 on request)
Housing Designs
- Pitch circle diameter
- Round flange
- Square flange
- Foot
Mounting Positions
- Any mounting position.
- You can find the explanation of the mounting positions and the respective quantities of lubricant in the document Quantity of lubricant for gear units ID 441871
Lubricants and Maintenance
- Mineral lubricant CLP ISO VG 220
- Option: Synthetic lubricant CLP HC ISO VG 220
Under normal operating conditions no lubricant change is required for gear unit size C0 to C5 (lubricated for life).
We recommend a change of lubricant for gear unit size C6 to C9 after approx. 10,000 hours of operation.
"Bridge the Gap"
Based on this principle, STOBER has brought a new motor class to market:
- Up to 96% efficiency and thus IE5
- Higher acceleration capability than asynchronous motors
- Substantially lighter and more compact than asynchronous motors with a comparable rating
- Rugged thanks to absence of the encoder
- Regulation of speed and torque at low speeds and when stalling
- Only a standard power cable is required without any additional cores or shielding
- Rotating plug connector with quick lock
- Spring-loaded holding brake (optional)
Your Bridge to Greater Efficiency
With up to 96 percent efficiency, the STOBER lean motor corresponds to the IE5 efficiency class. Asynchronous motors usually only achieve similar efficiency by using more or higher quality materials, like copper. These motors end up being significantly larger and heavier as a result. The future-proof Lean motors allow engineers to design smaller drives, dimension the machine itself smaller and reduce the installation area. Users save energy and reduce the costs for the components. Compared to an asynchronous motor with incremental encoder, the Lean motor can regulate more dynamically and efficiently thanks to its greatly reduced flywheel mass.
STOBER has it under control: Lean in the system
The STOBER Lean motor allows for variable regulation of speed and torque from a standstill to maximum speed with full torque control. Despite not having an encoder in the motor, the speed deviation is less than 1%, while the positioning accuracy is ±1°. The position and speed are determined in combination with the STOBER SC6 and SI6 drive controllers. The controllers have a very compact design, so users can reduce costs in procurement, commissioning and maintenance—and have more design flexibility at the same time.
- SI6 with power range from 0.75 to 25.9 kW
- SC6 with power range from 0.75 to 11 kW
For more information, see Drive Controllers
Less is more: A standard power cable is all you need!
The position of the encoderless motor is determined using the power connection terminals. This means that a STOBER standard power cable can be used without any additional cores or shielding. This reduces installation effort considerably.
A Robust and Less Expensive Alternative
The Lean motor provides an alternative to versatile synchronous servo motors that is approximately 30% more cost-efficient. It is also much more rugged since no electronics are installed in the motor. As a result, the Lean motor is well-suited to automation tasks that are exposed to high vibrations and oscillations.
Optional
The Lean motor is available in combination with many STOBER gear units.
You have the option of receiving the motors with a rugged spring-loaded holding brake, which provides high braking performance throughout the entire service life.
Winding Protection
PTC thermistors are installed in STOBER synchronous servo motors as a configuration feature to implement thermal winding protection. This makes it possible for the motor to exceed the maximum permitted winding temperature with the appropriate devices turned off.
Paint Finish
Black RAL 9005
Type |
Ratio |
Max. perm. acceleration torque [Nm] |
Stall torque on the gear unit output [Nm] |
Max. perm. input speed in cyclic operation [1/min] |
Backlash [arcmin] |
Torsional stiffness [Nm/arcmin] |
C002 |
2 – 25 |
8.7 – 72 |
4.7 – 68 |
6000 |
16 – 20 |
1.3 – 1.6 |
C102 |
2 – 56 |
17 – 138 |
9.2 – 137 |
5000 – 6000 |
15 – 18 |
3.1 – 3.9 |
C202 |
2 – 70 |
48 – 230 |
23 – 230 |
4500 – 6000 |
14 – 17 |
6 – 8.3 |
C203 |
81 – 92 |
230 |
187 – 215 |
6000 |
14 |
8.3 |
C302 |
3.1 – 35 |
124 – 400 |
64 – 372 |
4500 – 5500 |
13 – 16 |
7.1 – 8.7 |
C303 |
81 – 137 |
350 – 400 |
189 – 350 |
5500 |
13 |
8.7 |
C402 |
3.9 – 56 |
156 – 600 |
80 – 548 |
4000 – 5000 |
12 – 15 |
17 – 22 |
C502 |
4.6 – 70 |
185 – 920 |
95 – 903 |
4000 – 4500 |
12 – 14 |
21 – 23 |
C503 |
81 |
920 |
776 |
4500 |
12 |
23 |
C612 |
20 – 55 |
783 – 1380 |
404 – 1310 |
4000 |
10 |
74 |
C613 |
49 – 135 |
913 – 1650 |
730 – 1561 |
4000 |
10 |
74 |
C712 |
25 – 70 |
1011 – 2121 |
522 – 2010 |
3600 |
10 |
122 |
C713 |
81 – 132 |
2256 – 2760 |
1646 – 2690 |
3600 |
10 |
122 |
C813 |
79 – 178 |
2486 – 4140 |
1613 – 3625 |
3400 |
10 |
204 |
C Series
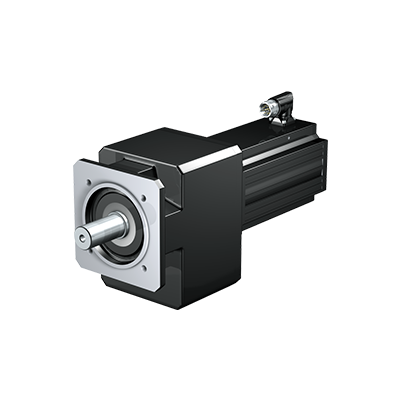
- 产品简介
- 产品特点
- 产品规格
- 产品尺寸
- 资料下载
- Solid shaft with key
- Solid shaft without key (C0 - C5, starting at C6 on request)
Housing Designs
- Pitch circle diameter
- Round flange
- Square flange
- Foot
Mounting Positions
- Any mounting position.
- You can find the explanation of the mounting positions and the respective quantities of lubricant in the document Quantity of lubricant for gear units ID 441871
Lubricants and Maintenance
- Mineral lubricant CLP ISO VG 220
- Option: Synthetic lubricant CLP HC ISO VG 220
Under normal operating conditions no lubricant change is required for gear unit size C0 to C5 (lubricated for life).
We recommend a change of lubricant for gear unit size C6 to C9 after approx. 10,000 hours of operation.
"Bridge the Gap"
Based on this principle, STOBER has brought a new motor class to market:
- Up to 96% efficiency and thus IE5
- Higher acceleration capability than asynchronous motors
- Substantially lighter and more compact than asynchronous motors with a comparable rating
- Rugged thanks to absence of the encoder
- Regulation of speed and torque at low speeds and when stalling
- Only a standard power cable is required without any additional cores or shielding
- Rotating plug connector with quick lock
- Spring-loaded holding brake (optional)
Your Bridge to Greater Efficiency
With up to 96 percent efficiency, the STOBER lean motor corresponds to the IE5 efficiency class. Asynchronous motors usually only achieve similar efficiency by using more or higher quality materials, like copper. These motors end up being significantly larger and heavier as a result. The future-proof Lean motors allow engineers to design smaller drives, dimension the machine itself smaller and reduce the installation area. Users save energy and reduce the costs for the components. Compared to an asynchronous motor with incremental encoder, the Lean motor can regulate more dynamically and efficiently thanks to its greatly reduced flywheel mass.
STOBER has it under control: Lean in the system
The STOBER Lean motor allows for variable regulation of speed and torque from a standstill to maximum speed with full torque control. Despite not having an encoder in the motor, the speed deviation is less than 1%, while the positioning accuracy is ±1°. The position and speed are determined in combination with the STOBER SC6 and SI6 drive controllers. The controllers have a very compact design, so users can reduce costs in procurement, commissioning and maintenance—and have more design flexibility at the same time.
- SI6 with power range from 0.75 to 25.9 kW
- SC6 with power range from 0.75 to 11 kW
For more information, see Drive Controllers
Less is more: A standard power cable is all you need!
The position of the encoderless motor is determined using the power connection terminals. This means that a STOBER standard power cable can be used without any additional cores or shielding. This reduces installation effort considerably.
A Robust and Less Expensive Alternative
The Lean motor provides an alternative to versatile synchronous servo motors that is approximately 30% more cost-efficient. It is also much more rugged since no electronics are installed in the motor. As a result, the Lean motor is well-suited to automation tasks that are exposed to high vibrations and oscillations.
Optional
The Lean motor is available in combination with many STOBER gear units.
You have the option of receiving the motors with a rugged spring-loaded holding brake, which provides high braking performance throughout the entire service life.
Winding Protection
PTC thermistors are installed in STOBER synchronous servo motors as a configuration feature to implement thermal winding protection. This makes it possible for the motor to exceed the maximum permitted winding temperature with the appropriate devices turned off.
Paint Finish
Black RAL 9005
Type |
Ratio |
Max. perm. acceleration torque [Nm] |
Stall torque on the gear unit output [Nm] |
Max. perm. input speed in cyclic operation [1/min] |
Backlash [arcmin] |
Torsional stiffness [Nm/arcmin] |
C002 |
2 – 25 |
8.7 – 72 |
4.7 – 68 |
6000 |
16 – 20 |
1.3 – 1.6 |
C102 |
2 – 56 |
17 – 138 |
9.2 – 137 |
5000 – 6000 |
15 – 18 |
3.1 – 3.9 |
C202 |
2 – 70 |
48 – 230 |
23 – 230 |
4500 – 6000 |
14 – 17 |
6 – 8.3 |
C203 |
81 – 92 |
230 |
187 – 215 |
6000 |
14 |
8.3 |
C302 |
3.1 – 35 |
124 – 400 |
64 – 372 |
4500 – 5500 |
13 – 16 |
7.1 – 8.7 |
C303 |
81 – 137 |
350 – 400 |
189 – 350 |
5500 |
13 |
8.7 |
C402 |
3.9 – 56 |
156 – 600 |
80 – 548 |
4000 – 5000 |
12 – 15 |
17 – 22 |
C502 |
4.6 – 70 |
185 – 920 |
95 – 903 |
4000 – 4500 |
12 – 14 |
21 – 23 |
C503 |
81 |
920 |
776 |
4500 |
12 |
23 |
C612 |
20 – 55 |
783 – 1380 |
404 – 1310 |
4000 |
10 |
74 |
C613 |
49 – 135 |
913 – 1650 |
730 – 1561 |
4000 |
10 |
74 |
C712 |
25 – 70 |
1011 – 2121 |
522 – 2010 |
3600 |
10 |
122 |
C713 |
81 – 132 |
2256 – 2760 |
1646 – 2690 |
3600 |
10 |
122 |
C813 |
79 – 178 |
2486 – 4140 |
1613 – 3625 |
3400 |
10 |
204 |